Quality Management
MERRY's customers evaluate MERRY through their scorecard mechanism or by MERRY's proactive annual satisfaction surveys. These methods help understand customers' evaluations, opinions, and needs. The gathered information is analyzed to identify root causes, develop improvement plans, and actively implement and track the results.
The issues from customer scorecards and satisfaction surveys are consolidated and forwarded to the relevant responsible units for root cause analysis and to propose improvement plans within a set timeframe. These responses are then sent back to the business unit. Besides replying to the customers, the business unit also forwards the information to the audit unit and the overseas plant marketing units for subsequent tracking and improvement. Both the satisfaction surveys and the scorecard mechanism cover four major aspects: "Quality, R&D, Procurement, and Integration." These aspects serve as important reference indicators for improving subsequent related operations and business performance. The overall customer satisfaction in 2023 was 83.21, approximately equal to the 83.16 in 2022.
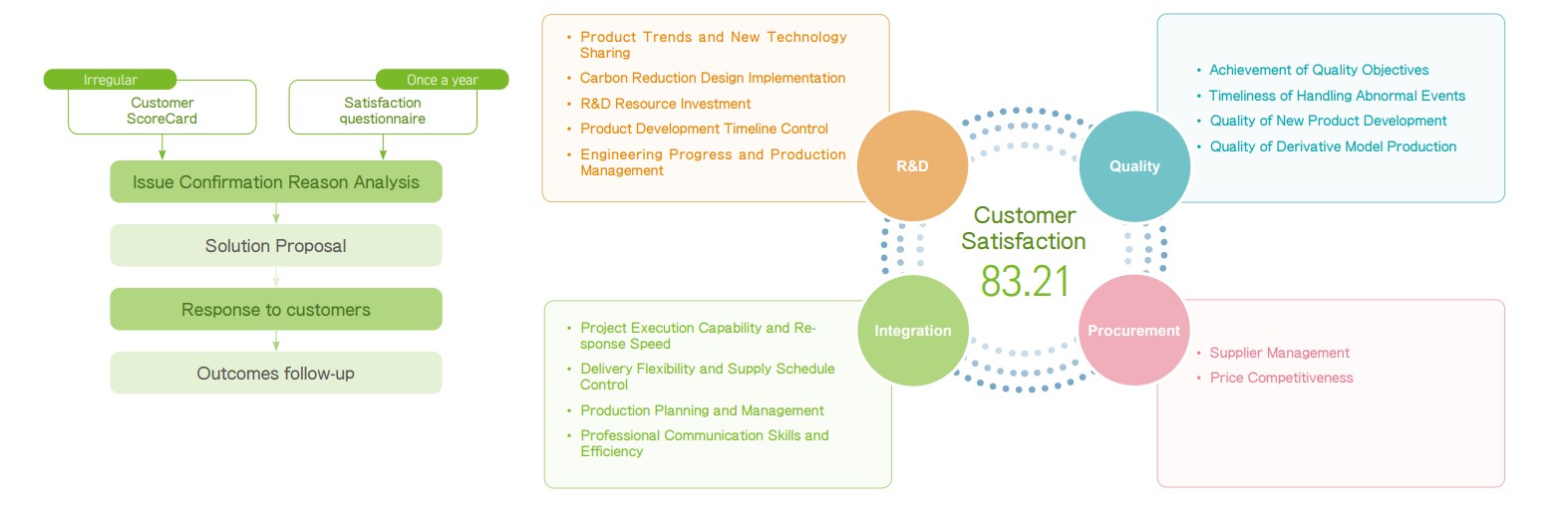
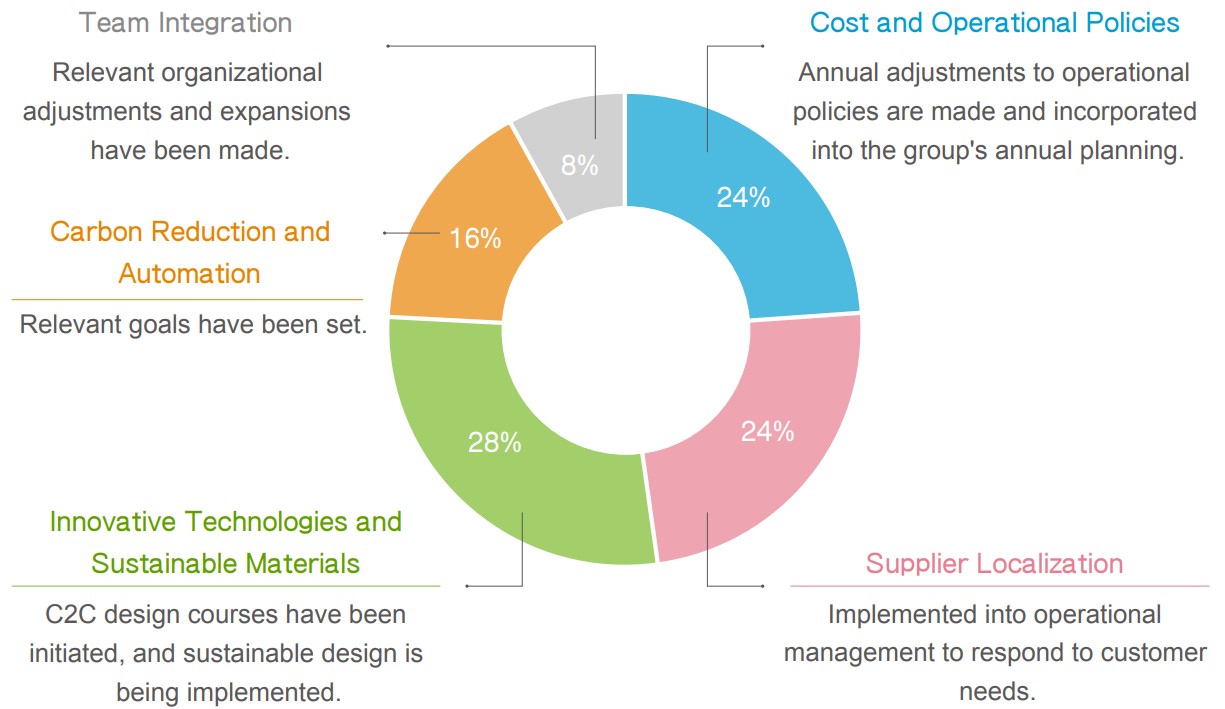
Quality Management System
MERRY has established a systematic process for product development to ensure that the quality, cost, and delivery time of new products meet customer and market demands within the system framework. This continuous pursuit of process optimization aims to enhance product competitiveness. The quality assurance system involves collaborative execution by cross-functional teams, including R&D personnel, quality management staff, sales, production sites, and supply chain management. Through the cycle of planning, implementing, checking, and improving, MERRY optimizes Quality Management and Customer Service Optimization.
Key Materials Management Procedures
To enhance the efficiency of new project development and customer satisfaction, MERRY has established the "Key Material Definition and Operation Procedures." This defines and evaluates the parts that constitute a product, particularly those that require special control due to their impact on production quality. The goal is to ensure quality and delivery time management at each development stage, as well as the quality of trial production and mass production.
Digital Optimization
All industries face the challenge of delivering information to customers more quickly. Companies must adapt to this highly volatile era by accelerating their comprehensive digital transformation efforts. MERRY initiated its digital transformation in 2021, introducing innovative models such as process robots in production management and global digital supply chain management. Through digital optimization, MERRY also enhances customer relationship management. Given MERRY's high customer concentration, the company implements twoway electronic data exchange based on revenue proportion and transaction frequency to optimize service processes.